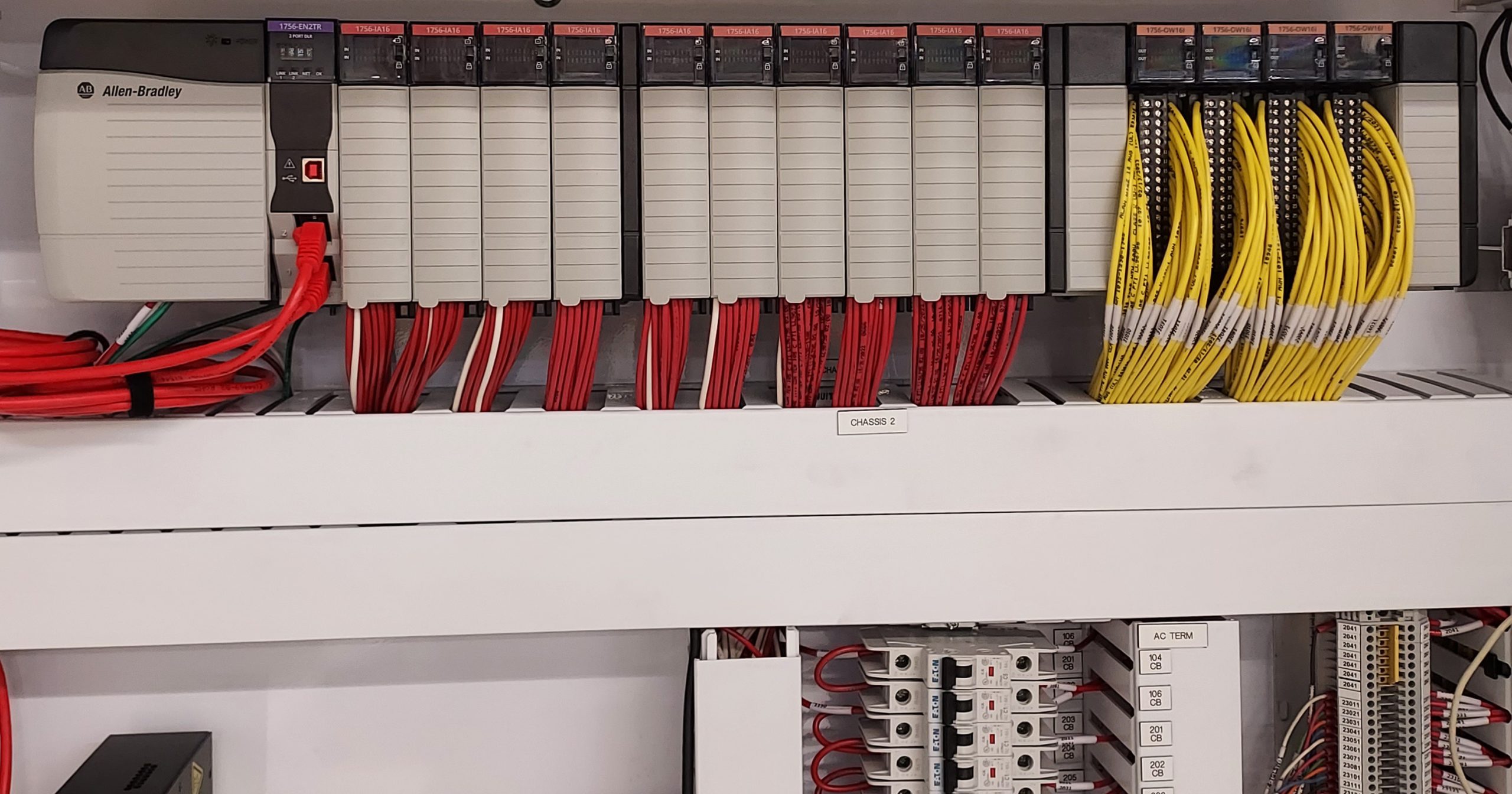
Controlling the Water: Wichita’s Northwest Water Facility
May 20, 2025
Water treatment probably isn’t something most people give much thought to on a daily basis, but MKEC’s instrumentation and controls team recently spent a lot of time thinking about water treatment.
The City of Wichita’s new Northwest Water Facility (NWWF) is set to open later this year, increasing Wichita’s water treatment capacity to 120 million gallons of water a day to meet the growing city’s water needs. Each day, every gallon will go through the water treatment process in a facility that includes thousands of valves, pumps, and transmitters controlled from a central control room.
Attention to Detail
Our instrumentation and controls team worked with Wichita Water Partners and R.E. Pedrotti to set up the instrumentation and controls system, and it was a large job that required focused attention to even the smallest details.
“Every single piece of equipment has to have a control system to tell it what to do,” says Scott Davids, electrical engineer for MKEC. “A valve is a perfect example. You have to have an open command, close command, open indication and closed indication. Each device has to be wired to a controller, and a program has to be written to control that device.”
Years ago, valves were manually operated and motors were started and stopped with pushbutton stations, but now those valves and motors are operated remotely from a control room. That means every one of those connections has to be wired and tested.
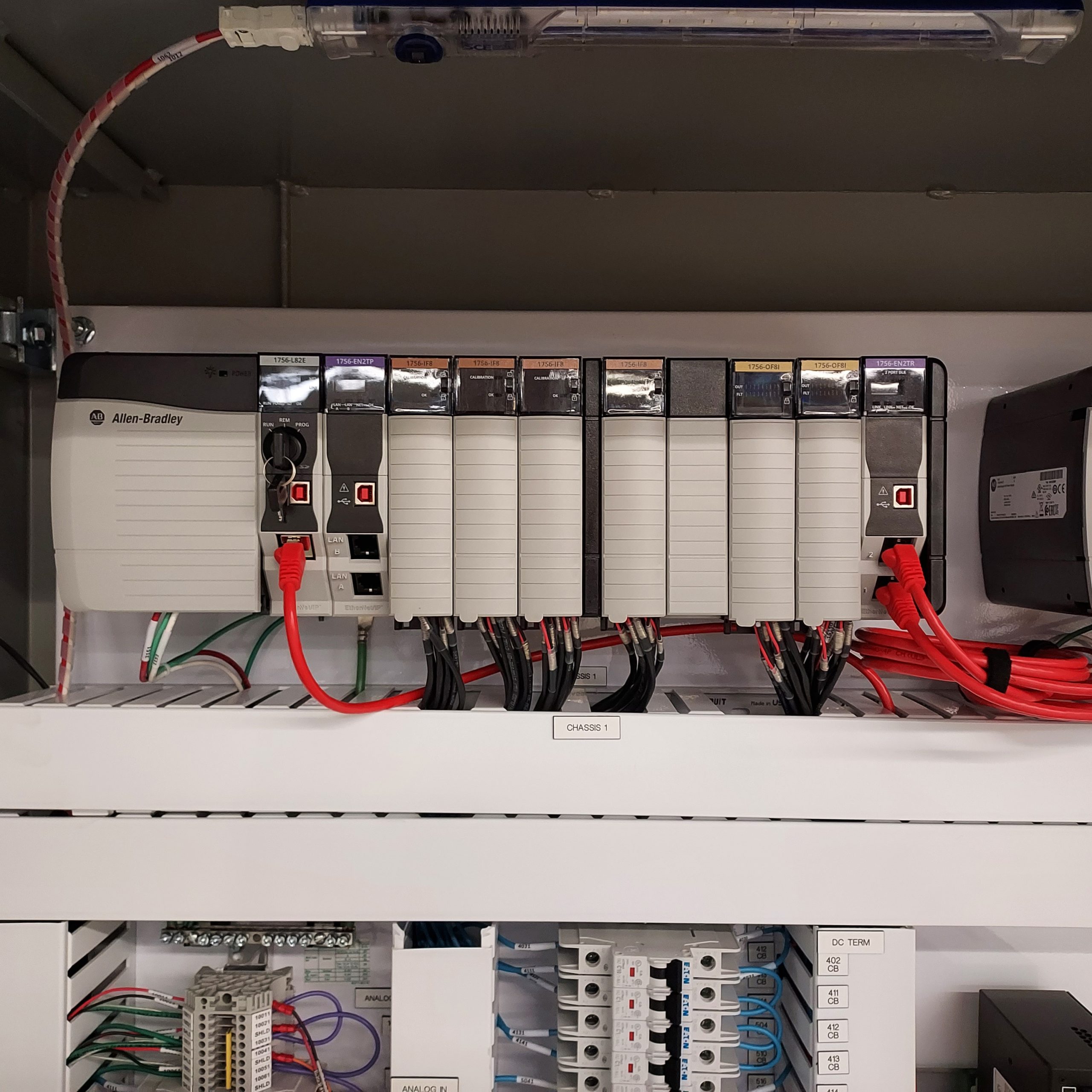
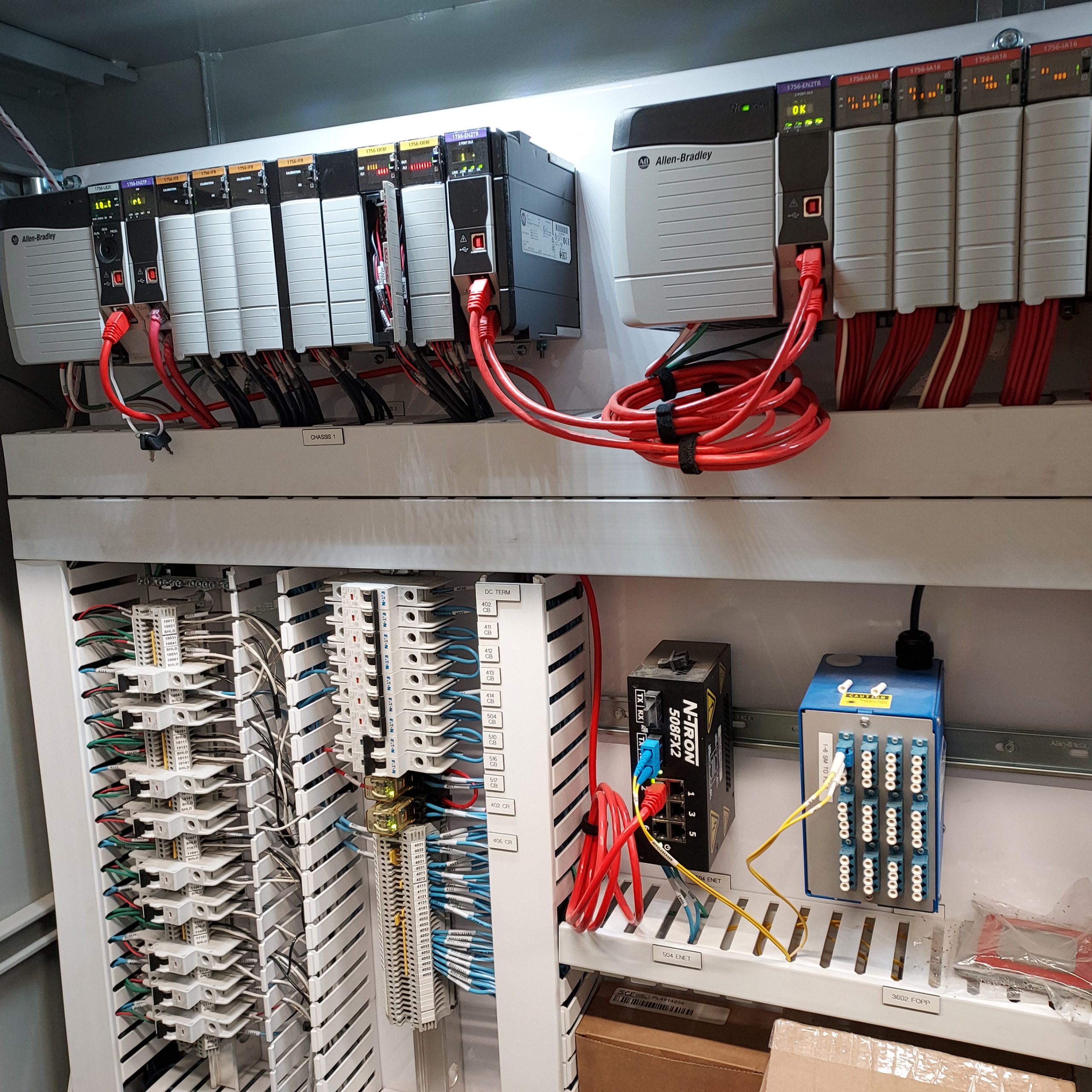
Each device is wired to a programmable logic controller (PLC), which is controlled by a human machine interface (HMI).
“The HMI gives visualization to the entire process,” Davids says.
Operators in the control room have to be able to see the status of every instrument, motor, and valve to be able to run the plant.
“From their screens, they are able to set things like where the raw water comes from and what each valve will do,” Davids says. “This is critically important because this is how the operators operate the entire facility. It’s their window to monitor the process and their means of controlling the process.”
Testing the Waters
MKEC’s team wasn’t just responsible for programming the PLC and HMI. We also worked with our partners to test the system.
“We verify every single thing that is wired to the PLCs,” Davids says. “For a switch, we verify that the wiring is correct then we close the switch and make sure the PLC sees that the switch is closed, and that the HMI indicates that it is closed. Then we do the reverse from the HMI to the PLC to the valve. You have to go one by one, and someone physically checks if the valve is open or closed. There are literally thousands of individual points that have to be tested.”
The testing process for the NWWF took around nine months.
“You can only do one test at a time,” Davids says. “You have resources dedicated for long periods of time.”
In addition, some valves have more than just an open and shut position. They modulate between open and closed, which requires a different type of testing to verify each position. All of this testing takes place before water is ever introduced to the system.
Once water entered the facility, MKEC worked with Wichita Water Partners and R.E. Pedrotti to test the functionality and capacity of the system. The entire testing process took about 18 months.
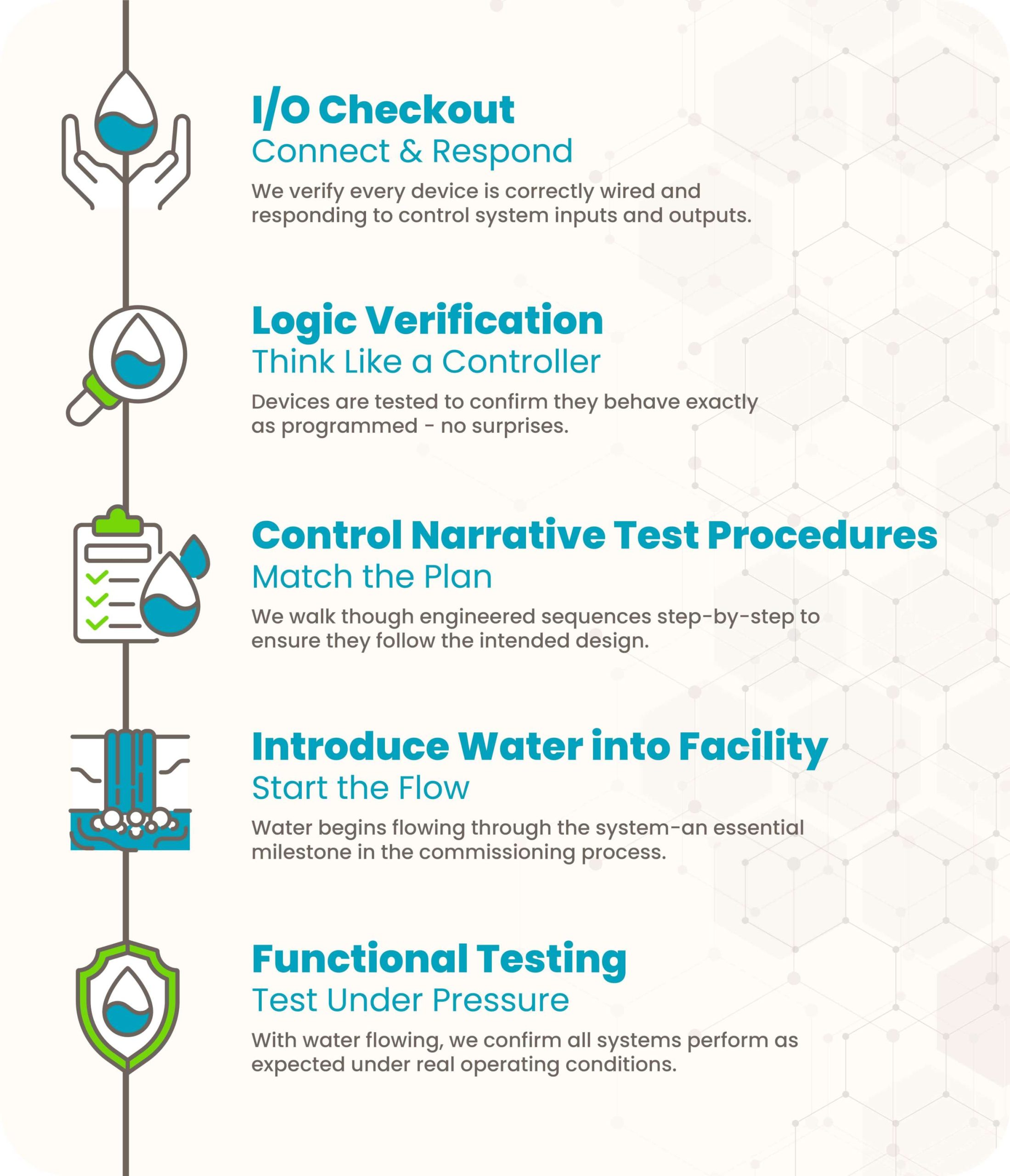
Working Together
To bring a project on the scale of the NWWF to life takes coordination between all the contractors and stakeholders.
“It took a lot of coordination,” Davids says. “Obviously, we couldn’t do all of the testing all by ourselves. It required a team. Wichita Water Partners had resources assigned to each area, who were responsible for that area. They did a really good job of that, and things went fairly smoothly. A lot of times on big jobs like this, it’s not uncommon to spend days waiting for things to be available to test, but we didn’t experience that on this job.”
Since MKEC was solely responsible for the design of the residual handling area, this included instrument design and writing the control narrative, the document that describes how a control system is expected to operate under different conditions.
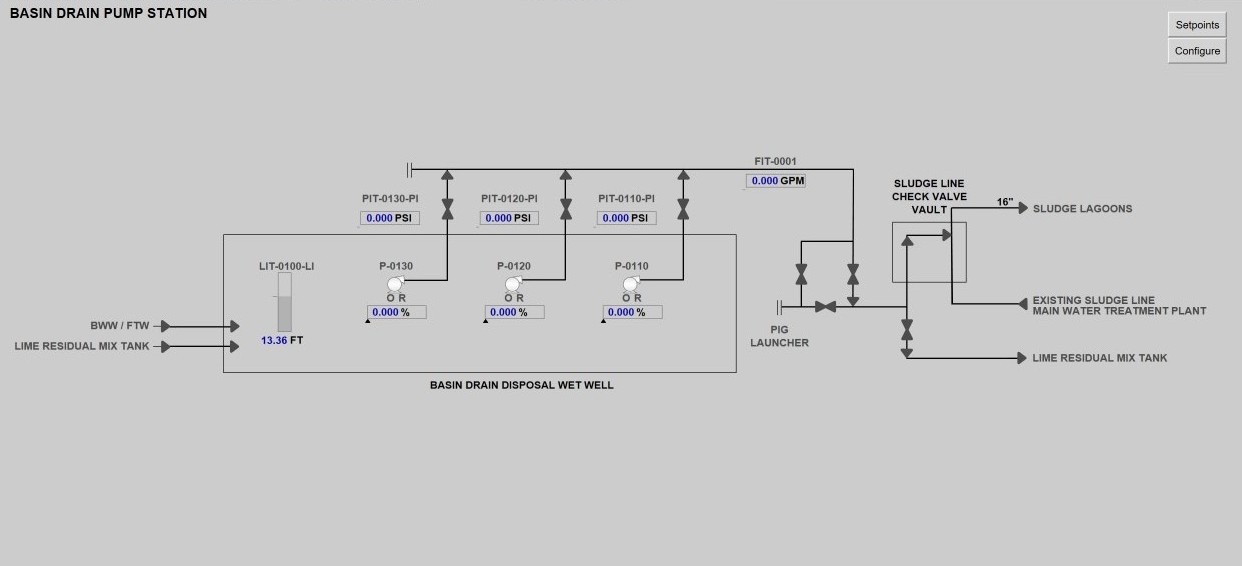
Overcoming Challenges
No project is without its challenges, and this project was no different. The chemical building area contains three vendor-supplied systems: a lime system, a soda ash system, and a carbon dioxide system. Each system came from a different vendor, but we needed to communicate status and commands for each system.
“Each vendor did things slightly differently,” Davids says. “Working out the communications for each vendor system was one of our biggest challenges.”
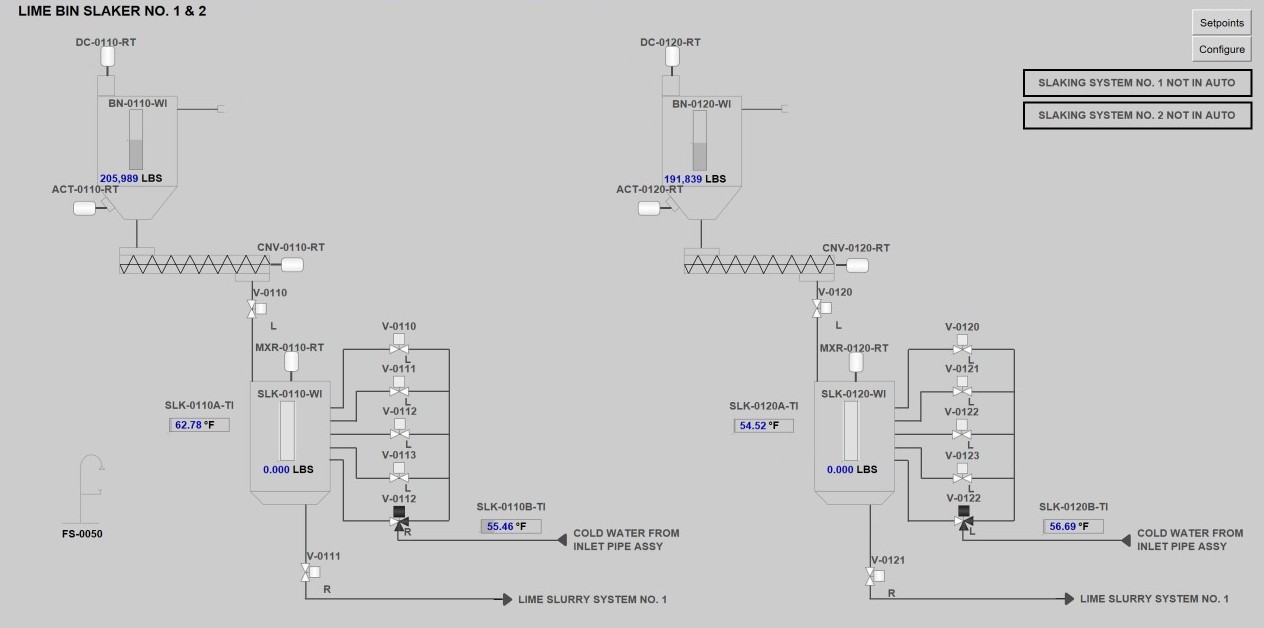
Providing Clean, Safe Water
We’re proud of the work we did on this project that will serve over 500,000 Kansans in the Wichita area. As a part of the Wichita community, MKEC understands the importance of providing safe, clean water to everyone who lives within the area.
With our attention to detail, our willingness to collaborate, and our determination to overcome challenges, we’re committed to providing each of our clients with quality engineering services, and we think our instrumentation and controls team embodied that spirit on this project.
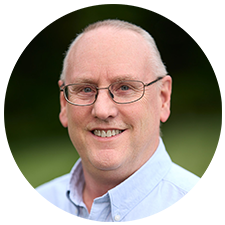
“If you’re making something the entire city is going to consume, you have to make sure that everything is right.”
Scott Davids, Electrical Engineer